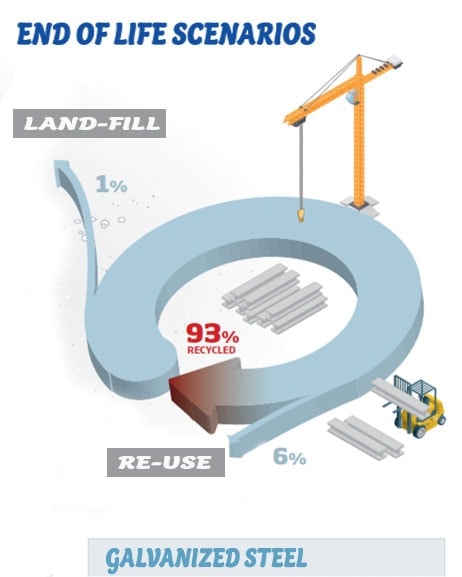
There seems to be a lot of confusion about the sustainability and longevity of galvanizing –
Galvanizing Process. Hot-dip galvanizing is the process of immersing iron or steel in a bath of molten zinc to produce a corrosion resistant, multi-layered coating of zinc-iron alloy and zinc metal. The process is inherently simple, which is a distinct advantage over other corrosion protection methods. This Cathodic protection prevents corrosion by converting all of the anodic (active) sites on the metal surface to cathodic (passive) sites by supplying electrical current (or free electrons) from an alternate source. Usually, this takes the form of galvanic anodes, which are more active than steel.
Build it and forget it!
When looking to build a new structure galvanizing makes sense, painting steel creates an ongoing maintenance scenario. With galvanizing it’s an almost build it and forget it scenario, because of the longevity of the galvanized coating and the way it performs for 50, 75 to 100 years or more, without maintenance means using fewer resources throughout the life of the structure to maintain it, both from an environmental standpoint and economic standpoint. Your not spending money on maintenance or wasting resources to replace it.
Creating a maintenance free structure that is both environmental and economical makes galvanizing the most sustainable product created out of natural materials. both Zinc and iron are natural metal that is 100% recyclable without losing any properties. So can be used again and again, creating an infinitely renewable resource.
Hot-dip galvanized steel is a sustainable infinitely renewable building material that improves the quality of life of the project is both durable for generations without constant maintenance programs, saving both time and money in both the private and public sectors. It uses Zinc – the healthy metal and we need to encourage builders, and those who specify gal – that if they want to do it once and do it right – choose Galvanizing.